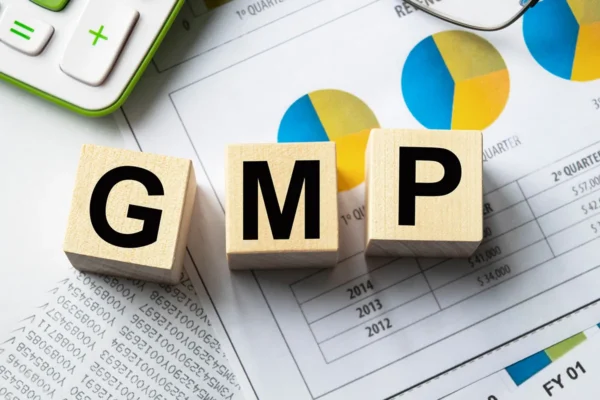
Bridging GMP and GDP: Ensuring Cold Chain Integrity from Manufacturing to Distribution:
In the pharmaceutical industry, maintaining the quality of temperature-sensitive products requires strict adherence to both Good Manufacturing Practices (GMP) and Good Distribution Practices (GDP). GMP ensures medicines are produced in a controlled environment, free from contamination, while GDP ensures that the same care is maintained during storage and distribution. However, transitioning from manufacturing to distribution, especially in cold chain logistics, presents challenges where temperature fluctuations can compromise product integrity. Bridging GMP and GDP requires an integrated approach that focuses on monitoring, risk management, and collaboration among manufacturers, logistics providers and regulators.
Understanding GMP in Cold Chain Management
GMP regulations ensure that pharmaceuticals are consistently produced to quality standards. For temperature-sensitive products, GMP focuses on validated processes, proper packaging, labeling and strict quality control. Manufacturers conduct stability studies to determine the proper storage and transportation conditions for each product, which are reflected in storage labels such as “Store at 2°C–8°C” or “Keep below -20°C.” To meet these requirements, manufacturing facilities must have validated cold storage areas, backup power systems to prevent temperature excursions and automated temperature monitoring systems for real-time alerts.
Packaging plays a vital role in maintaining the required temperature during transit. Cold chain packaging solutions include insulated containers, phase-change materials (PCM) and dry ice for short-distance transport, as well as refrigerated trucks, temperature-controlled air cargo containers, and portable refrigeration units for longer distances. Clear labeling ensures proper handling, with details on storage conditions, handling instructions (e.g., “Do not freeze”), expiration dates and batch numbers for traceability.
Before shipment, cold chain products undergo strict quality control checks to ensure they were stored under validated conditions, that the packaging meets insulation and durability requirements and that temperature monitoring devices are included in each shipment to track any temperature deviations. Once the product leaves the manufacturing facility, the responsibility shifts to the distribution network, where GDP regulations take over.
The Role of GDP in Cold Chain Distribution
GDP ensures that pharmaceutical products are stored, transported and handled properly, preventing any compromise to their quality. This is especially important for biologics, vaccines and other temperature-sensitive products that can degrade if exposed to temperature fluctuations. Under GDP, distributors must have temperature-controlled warehouses with automated monitoring and alarm systems. Logistics partners should have GDP-certified vehicles with cold chain expertise. Continuous temperature monitoring, using data loggers, GPS tracking and cloud-based reporting, ensures full visibility throughout transportation.
A risk-based distribution approach is also essential. Distributors must assess risks such as transit times, customs delays or extreme weather and ensure that cold storage is available at transfer points.
Emergency backup plans, with alternative routes and cold storage options, should also be in place. GDP regulations also require detailed documentation to maintain full traceability. Temperature records must be kept from departure to arrival and any deviations must be documented with corrective actions. While GMP ensures products leave the manufacturing facility in optimal condition, GDP ensures they arrive safely at their destination, maintaining the same standards.
Bridging GMP and GDP for a Seamless Cold Chain
To bridge GMP and GDP, pharmaceutical companies need to integrate manufacturing, logistics and regulatory compliance into a coordinated cold chain strategy. One critical aspect is end-to-end temperature monitoring. Temperature excursions can occur at any point in the supply chain, so continuous monitoring is crucial. Companies can implement IoT-enabled smart sensors, automated alert systems and cloud-based data logging for real-time temperature tracking and compliance reporting. Another important factor is qualification and validation across the entire supply chain. This includes validating cold chain transport to ensure that vehicles, shipping containers and packaging can maintain temperature stability. Route qualification studies must assess potential risks such as customs delays or exposure to extreme temperatures. Regular audits of suppliers and logistics partners ensure they comply with both GMP and GDP standards. Collaboration and training across different departments are also essential. Manufacturing and quality teams must understand GDP requirements to ensure proper handover of products, while logistics and distribution teams should be trained on GMP standards for cold chain handling. Joint audits and risk assessments between regulatory and compliance teams can align GMP and GDP expectations. Additionally, leveraging advanced technologies such as blockchain, AI-powered analytics and digital twin simulations can help optimize cold chain logistics, enhance compliance and increase transparency.
Conclusion
Bridging GMP and GDP is crucial for maintaining cold chain integrity in pharmaceutical products. By integrating real-time monitoring, risk-based logistics planning and cross-functional collaboration, companies can reduce temperature excursions, ensure regulatory compliance, and safeguard patient health. The future of cold chain logistics lies in automation, AI and blockchain-based traceability, creating a more resilient and transparent supply chain. Companies that successfully bridge GMP and GDP will not only meet regulatory standards but also gain a competitive advantage in the evolving pharmaceutical industry.